Telematics Maintenance: Predicting the Future
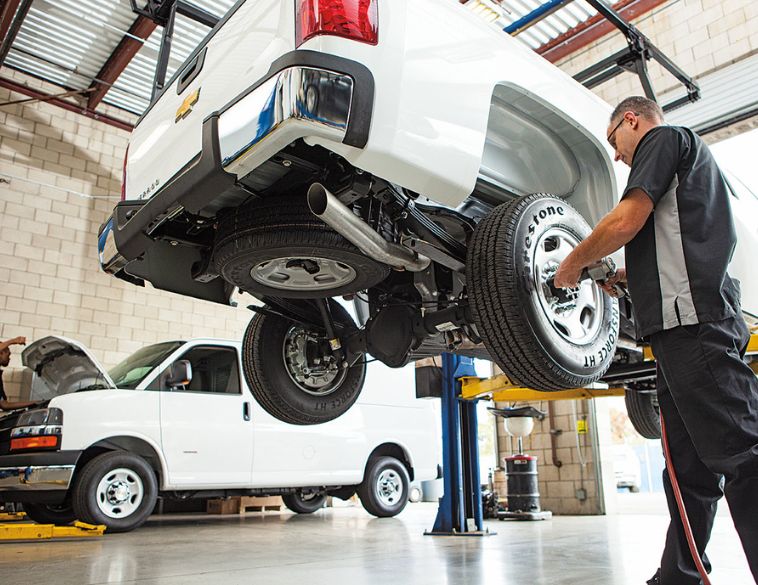
Today’s advanced technologies can help fleet managers cut maintenance costs, reduce downtime and prevent breakdowns.
While fleet professionals often think of telematics as a must when managing driver behaviour or planning the most efficient routes, today’s telematics solutions can do so much more. One of the areas where telematics can really shine is vehicle maintenance. Properly employed, telematics can help fleet managers better schedule maintenance stops, as well as prevent unexpected breakdowns.
“Fleets can significantly minimize their downtime by leveraging telematics to predict and schedule their maintenance needs accurately,” says Stephen White, Associate Vice President, Enterprise Sales at GEOTAB. “Technologies, such as remote diagnostics and predictive maintenance, play a crucial role. These tools analyze the fault codes and other vehicle data in near real time to predict maintenance requirements, thereby preventing unexpected breakdowns.”
These breakdowns, White explains, can be more costly than some fleet professionals may realize. “The first thing you’re going to avoid is the cost of the tow bill,” he says. “The more serious risk is that a truck or a vehicle that breaks down on the side of the road is a sitting duck. It’s a road hazard that someone can collide with. That’s why predictive maintenance is so critical.”
With telematics systems in place, fleet managers can receive comprehensive insights about the health of their vehicles. “This goes way beyond simply receiving alerts,” White adds. “The reports fleet managers receive enables them to prioritize and proactively schedule repairs. This strategy not only reduces downtime, but it also lowers maintenance costs by addressing issues before they escalate, and before they become a much larger and more expensive issue.”
The good news is that fleets don’t have to go overboard in terms of equipment purchases when all they want to do is monitor vehicle health and plan PM schedules. “In general,” says Guillaume Poudrier, President of Geothentic, “a basic installation with a basic device is enough to be able to manage maintenance. And actually, this is where you can have one of the biggest returns on investment.”
Remote diagnostic tools
Far from simply alerting the fleet manager that the engine light is on in one of their fleet vehicles, today’s telematics tools are way more advanced and sophisticated.
“We’re able to get critical diagnostic information from each vehicle’s computer,” White explains, “and by employing algorithms, we’re able to predict when an issue is about to happen. And if there is a malfunction and your MIL light—Malfunction Indicator Lamp—or check engine light goes on, we can tell remotely what the problem is, which gives the fleet manager the ability to tell the driver to pull over as soon as it’s safe to do so, or keep going because the problem can be handled at the next PM.”
This diagnosis, White adds, happens in as close to real time as possible. “We prefer to say ‘near real time,’ instead of ‘real time,’ because the only delay is the latency within the cellular networks, which is typically about three or four seconds. So, in near real time, we’re able to send an alert or an email or a text message to everyone in the company who was assigned to receive that kind of critical report. And if there’s no cellular network in the area, we can send the message via satellite.”
Telematics technologies can also be employed to pay attention to anomalies that might be indicative of a problem that’s about to happen. “There might be a specific vibration detected or an unusual fuel consumption trend,” Geothentic’s Poudrier explains. “By analyzing this data, we can predict an upcoming problem, and when we prevent the problem from occurring, we can save a lot of money.”
The advent of AI
It should come as no surprise that artificial intelligence (AI) is making its way into telematics. Armed with AI, telematics technologies are smarter and more capable than ever.
“One of the more noteworthy innovations in telematics is the introduction of enhanced predictive maintenance tools that use AI to forecast vehicle failures weeks in advance,” White explains.
While that’s impressive, it gets even better. White explains that fleet managers can now employ some of GEOTAB’s technologies to ask their AI-powered system questions like, “Which one of my vehicles is least efficient,” or, “What’s my most expensive vehicle to maintain,” or, “What are my top ten worst drivers?”
“It’s frightening just how accurate the answers are,” White notes. “It’s amazing when you consider what you can ask it, and the answers it will give you. It’s changing the way fleets are able to use data, because anybody can go in and ask it either a simple question or a detailed question, and get a very accurate answer back.”
Like all advanced technologies, AI makes things a bit easier, even for those who aren’t as tech-savvy or computer literate as they’d like to be. “You can ask it anything you can think of,” White explains, “and what’s nice is that you don’t have to be a data expert. The CEO of a company isn’t typically going to comb through thousands of Excel reports, but if they want to know what the average fuel economy of their fleet is, or what their maintenance costs have been for the past six months, they can just type that in and get the answer instantly.”
It’s not magic
As impressive as today’s telematics technologies may be, especially when you consider what AI-powered systems can do, Geothentic’s Poudrier warns that we can’t overestimate what the technology can do. When all is said and done, fleets still need capable human beings on the team in order do to the work that computers simply can’t.
“It’s not magic,” Poudrier says. “You still need people who can manage it, and you still need to implement changes in the habits of your employees. You also need a partner who can help with the implementation and who can support you so that you succeed.”
GEOTAB’s White offers the following advice for fleet professionals who are just getting started with telematics and want to better manage their maintenance needs.
“My advice is to begin with integrating telematics solutions that offer both remote diagnostics and predictive maintenance capabilities,” he concludes. “This integration will help in early identification and mitigation of potential issues, thereby reducing downtime and maintenance costs. They also need to train their staff to interpret and act on telematics data. Finally, regularly reviewing telematics reports, and then adjusting maintenance plans based on data insights, will then lead to much more efficient fleet operations.”