Counting the Cost of Tariffs
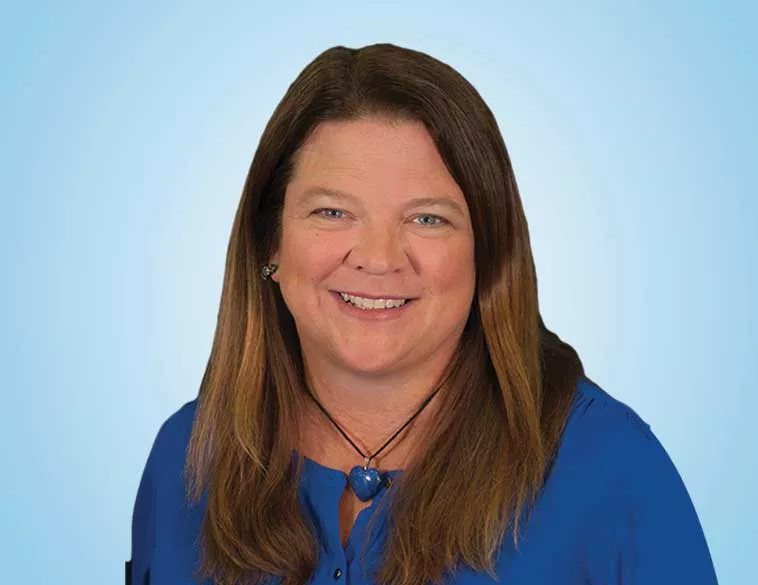
Here are a few alternatives to delaying replacement to help control fleet costs.
Fleet organizations have barely recovered from the pandemic where budgets were depleted to accommodate increased cleaning, workplace modifications, enhanced technology to allow work from home and many more changes.
The pandemic ended, but the fleet supply chain (vehicles and parts) did not rebound quickly. In fact, order times on many vehicle types are double that of pre-pandemic days. And now, a new source of uncertainty and potential price increases has arisen.
Tariffs being imposed by the United States government will have far-reaching impacts and organizations will be faced with difficult decisions on fleet retention and replacement. This would have been challenging any time, but coming so soon after the pandemic, the impact is multiplied.
Replace vs. repair
All good fleet managers know that you save money by replacing fleet vehicles on time, that is, at the end of their optimal lifecycle. In tough financial times, however, it is tempting to delay the replacement of vehicles. This strategy avoids costly capital replacement, but involves increases to maintenance, fuel costs and downtime. In the end, it costs organizations more, and there are better strategies that a fleet manager can use to save money and avoid delayed replacement.
Specifications: I recently worked with a fleet organization that boasted that their selected manufacturer called their ambulance specification a 13 out of 10 in terms of complexity. In another example, a Fire Department came under scrutiny for taking a standard specification and increasing costs by more than 40% by adding custom features, including a national flag in lights across the front grill.
Needs-based vs. wants-based specifications should be used so that money is spent on what matters. This is a complicated process, but the use of a specification development committee, an equipment needs survey of end-users, and the adherence to common specifications (including cooperative purchasing agreements) wherever possible will all help in cost containment.
Right-Sizing: Tracking fleet utilization and making data-fueled decisions will save an organization money. Conducting annual utilization reviews, and asking users to justify the retention of spares and lightly-used assets will help grow a mobility and cost-cutting mindset. Not only should the number of assets in the fleet be right-sized for the organization, but all assets should be right-typed for the function they serve.
Organizations should have policies in place for an annual review aimed at identifying assets that should be eliminated, replaced or right-typed. They should also seek opportunities to share or pool assets across departments. Finally, high-usage assets should be regularly rotated with lower-usage assets to balance utilization.
Mechanic Productivity: The industry average across government fleets is that mechanics are 70% productive. This means that, once breaks, vacations, sick leave and training are considered, a mechanic spends 70% of their time on the shop floor.
If an organization were to invest in a process review and improve productivity by five to 10 percent, savings will result. Process reviews often highlight inefficiencies, such as waiting for or having to leave the shop to pick up parts, shuffling vehicles between the shop and department locations, or taking vehicles to third-party maintenance providers.
A review will highlight activities that take mechanics off the shop floor and find better solutions to improve productivity. Shop mechanics will complete more work, and reduce downtime and/or work that must be outsourced (often to more expensive third parties).
It is inevitable that fleet managers are going to be asked to delay fleet replacement when times are tough. Those fleet managers need to ensure decision-makers fully understand that this is a short-term strategy with long-term cost implications. and that there are better ways to improve the efficiency of the operation.