Consider all the options before ordering your next box truck.
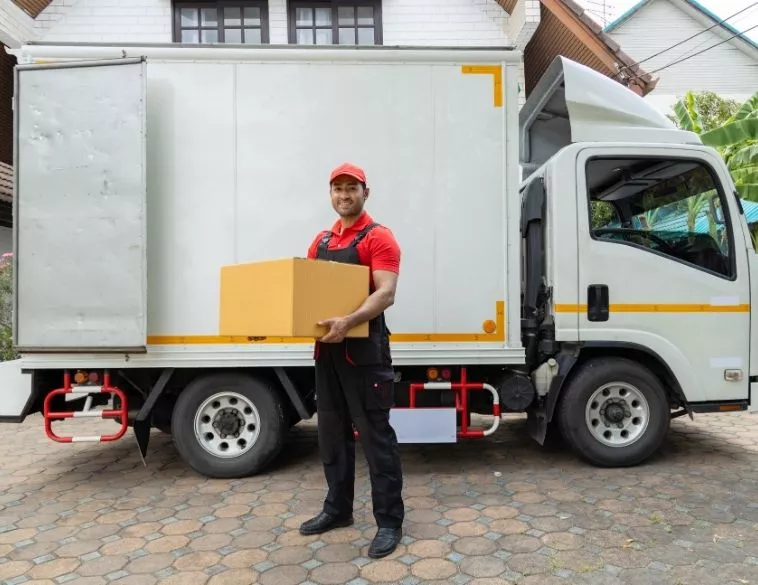
Consider all the options before ordering your next box truck.
If you’ve ever had to order a box truck and spec it yourself, you know how many choices you need to consider. Besides all the engine and chassis options, you’ll need to think about the box itself, and that alone can be a daunting task.
According to Brian Hickok, Strategic Business Advisor-Fleet at Element Fleet Management some of the most common choices fleet managers have to consider include the roof materials, liftgate types, lighting options, flooring materials, and much more.
“It really depends on the intended purpose or use of the truck,” Hickok says. “There are application guides and resources, as well as upfit truck application specialists, like here at Element, that can guide fleet professionals and make appropriate recommendations to help them choose the options that are compliant, and that will work best for each customer.”
Purpose built
Joe Birren, Regional Engineering Manager at Holman agrees that expert advice is a must. “My question, from the outset, is what’s the mission of the truck,” he says. “Is it for dry freight goods, is it last-mile delivery, is it refrigerated, and so on.”
Birren says that when he gets a call from a fleet manager who needs a new box truck, the first thing he does is stop by for a site visit. “I ride along to really understand how they are using the truck, how they are loading and unloading it,” he explains. “I also want to know about weight. If a customer tells me that they need to replace a particular truck, I’ll tell them to weigh it when it’s empty, then weigh it again when it’s loaded the way it would be on a normal day. That will help them see their payload weight.”
When it comes to the box itself, Birren notes that fleet managers need to decide which body structure is best. Depending on budget and weight requirements, the most common options include aluminum, fibreglass reinforced plywood, and composite materials.
Lighting options
If you’re operating primarily during the daytime, Birren adds, you can opt for a translucent roof. Otherwise, you would need to consider what kind of lighting you would like inside the box. If security is an issue, or if you’re in an area that gets a lot of hail, then an aluminum roof might be a better option.
“As far as lighting goes, you’ll need to decide how many lights you want and whether you want them to be motion-activated, or if you prefer a switch at the door,” Birren adds.
Furthermore, you’ll need to consider what kind of walls you want: full plywood, slat or exposed. “You also have to consider what kind of cargo management you need,” Birren adds. “If you require D-rings for tie-down straps to secure cargo to the floor, what kind of spacing do you require and for E-track, how many rows and at what height from the floor do they need to be installed?”
Another key consideration, he adds, is whether the truck needs to be dock height. “How do you plan to load and unload the truck,” he says. “Will you be driving a forklift into the body? If so, you’ll need to reinforce the floors and add scuff plates all around. It’s really ugly when you drive a forklift into a body that’s not designed for it.”
Birren recommends investing in a tread plate that can take some abuse. “Make sure you build up that threshold plate at the back where the door is,” he says. “If you’re going to be loading with a forklift, dropping the load into the body, and then people are going to move the load with a pallet jack into the body, it’s good to reinforce the back with a nice big tread plate that’s going to take the abuse.”
Door options
One of the reasons why Birren is a big fan of a ride along is because it allows him to see what kind of door, ramp and liftgate options make the most sense. “Maybe a side door is needed,” he explains. “Do you want access without having to open the rear cargo door? What kind of side door would you like? How far from the front of the body does it need to be? And what kind of steps would you like?”
Birren says that something as simple as a side door can make a big difference, but it’s a feature that you might not realize you need, unless you ride along with the truck driver to see how items are loaded or unloaded during their work day. “It’s easy to miss this kind of detail,” he adds, “and I often hear how much a side door would be appreciated by the driver because they wouldn’t always have to open the rear door. Also, a side door is a big benefit when you’re loading or unloading at the side of a street.”
Liftgate and rear door options
When it comes to liftgates, Birren explains that there are quite a few options to choose from. “You have the more common types, like a tuck-under liftgate, which can be stowed under the back of the truck. They’re typically only good up to about 5,500 lbs.”
A larger liftgate, like a rail-lift, is a good option if you need something that can handle more weight. For example, if you’re constantly unloading larger items like heavy machinery. Another option is a cantilever liftgate, which sits vertically against the back doors of the truck when not in use.
You’ll also have to decide between a swing-out or roll-up rear door. “Each have their benefits,” Birren says. “The swing-out doors can rotate all the way to the side of the truck, and they’re a good option when you need to optimize height because you don’t have to worry about space for the door to roll into. But if you’re loading within an alleyway or an area where cars are parked around you, swing-out doors can be an issue.”
Remarketing
Birren offers one final piece of advice for fleet managers: “Try to design a truck that other people will want to buy,” he concludes. “Stick to what’s common, what will likely be in demand, and try to avoid too much customization. For example, even if you only need an 18 or 22-ft. box, stick to 26 feet, since it’s a common size, and it will be a lot easier to sell.”